Benutzer:Elcap/MEMS
MEMS[Bearbeiten | Quelltext bearbeiten]

Mikro-Elektromechanische Systeme (Microelectromechanical systems), abgekürzt „MEMS“, bestehen aus strukturierten festen und beweglichen mechanischen Teilen, meist auf einem Halbleitersubstrat, mit Abmessungen im Mikrometerbereich. Sie sind elektromechanische Bauelemente für elektronische Schaltungen, keine integrierten Schaltungen (ICs), werden jedoch oft zusammen mit der Steuerungselektronik in einem Gehäuse geliefert. MEMS werden mit Fertigungsprozessen, die aus der Halbleitertechnologie stammen, hergestellt. Mit ihnen werden unter anderem beispielsweise variable Kondensatoren, schwingende Träger, Hebel, Membranen, elektrische Schalter, rotierende Räder und einstellbare bewegliche Spiegel in Kleinstabmessungen realisiert. Diese Teile ergeben üblicherweise Sensoren, die elektrische Signale für elektronische Schaltungen zur Weiterverarbeitung liefern oder Aktuatoren, die durch elektronische Schaltungen angesteuert und bewegt werden können.
Begriffe[Bearbeiten | Quelltext bearbeiten]
Im deutschen Sprachraum werden drei hierarchisch geordnete Begriffe verwendet:
Die Mikrotechnik (auch Mikrostrukturtechnik) befasst sich mit Verfahren, die zur Herstellung von Körpern und geometrischen Strukturen mit Dimensionen im Mikrometerbereich (0,1–1000 µm) angewandt werden. Bei Strukturgrößen unter 100 nm redet man von Nanotechnik.
Die Mikrosystemtechnik (MST, micro systems technology), oder auch Mikrosystemtechnologie, ist ein Teilbereich der Mikrotechnik und ist die Lehre von der Entwicklung der Mikrosysteme und von den Techniken zu deren Realisierung. Dabei werden beispielsweise mikromechanische oder mikrooptische Bauelemente mit mikroelektronischen Schaltungen in einem komplexen System kombiniert und integriert.
Mikro-Elektromechanisches Systeme (MEMS) und Mikro-Opto-mechanische Systeme (MOEMS) sind Bauelemente deren Teile Abmessungen im Mikrometerbereich haben. MEMS haben mechanische, elektrische, fluidische oder chemische Funktionalität, MOEMS haben mechanische, elektrische und optische Funktionalität auf kleinster Fläche. Sie wirken meist mit Integrierten Schaltungen (Prozessoren) als System zusammen.
Bei Strukturgrößen <100 nm werden diese Bauelemente "Nano-Elektromechanische Systeme (NEMS)" (nanoelectromechanical systems (NEMS)) genannt.
Im englischen Sprachraum werden die Begriffe „Micro systems technology“ und „Microelectromechanical systems“ oft mit den Bauelementen „MEMS“ und „MOEMS“ gleichgesetzt. Im japanischen wird dafür der Begriff „Micromachines“ verwendet.
Funktionsumfang und Anwendungen[Bearbeiten | Quelltext bearbeiten]

MEMS-Sensoren und -Aktuatoren sind mehr als nur miniaturisierte „Makrosysteme“, die mit konventionellen diskreten Bauelementen aufgebaut sind. Denn die miniaturisierten Strukturen haben ein großes Verhältnis von Oberfläche zu Volumen. Dadurch sind Umgebungskräfte, (z. B. elektrostatischen Aufladung, Magnetisches Dipolmoment, Oberflächenspannung und Viskosität von Flüssigkeiten, Beschleunigung von Massen) leichter und schneller zu detektieren, als bei Makrosystemen. Sie besitzen folglich in Bezug auf die beteiligten physikalischen Effekte eine weitaus höhere Komplexität als rein elektronische Systeme.[1] MEMS-Bauelemente vereinigen über mechanische Funktionen hinaus auch elektrische, fluidische, optische oder chemische Funktionalität auf kleinster Fläche. MEMS grenzen im Nano-Maßstab an der molekularen Nanotechnologie mit ihren Nano-Elektromechanischen Systemen (NEMS), bei denen allerdings wegen der noch kleineren Abmessungen chemische und physikalische Vorgänge der Oberflächenchemie mit berücksichtigt werden müssen.
MEMS-Bauelemente haben einen geringen Energieverbrauch und bieten ein großes miniaturisiertes Funktionsspektrum mit schnellen Reaktionszeiten. Sie ermöglichen autonome Systeme und eine große Kostenersparnis bei der Realisierung von Schaltungen. Typisch für Anwendungen von MEMS- Sensoren und -Aktoren ist ihre Zusammenarbeit mit elektronischen Steuerungen (Prozessoren) in einer Vielzahl von Geräten in Bereichen wie der Informationstechnik, Elektrotechnik, Verkehrstechnik, Informatik, Biotechnologie und Medizintechnik. Eines der größten Anwendungsbereiche sind Beschleunigungs- und Drehsensoren (Gyroskope) im Automobilbereich für die Auslösung von Airbags und Überrollbügel, in Handhelds wie Smartphones zur Lageerkennung, in Digitalkameras zur Bildstabilisation und in Flugdrohnen zur Lagestabilisation. Anwendungen von MEMS mit Flüssigkeiten finden sich in der Mikrofluidik mit den Bubble-Jet-Druckköpfen moderner Drucker. MEMS-Elemente werden außerdem in der Akustik als Schalldruckwandler in MEMS-Mikrophone verwendet, in elektronischen Schaltungen finden sich MEMS-Oszillatoren zur Erzeugung von Frequenzen und in der Übertragungstechnik kommen sogenannte RF-MEMS zur Selektion von Sendefrequenzen zum Einsatz. Optische Anwendungen für MEMS, genannt MOEMS (Mikro-Opto-mechanische Systeme) sind beispielsweise Mikrospiegelaktoren in Videoprojektoren.
MEMS-Elemente sind wichtige Bestandteile der aktuellen Diskussion über das „Internet der Dinge“ (Internet of the Things (IoT)).[2]
Materialien und Prozesse für die MEMS-Fertigung[Bearbeiten | Quelltext bearbeiten]
Zur Herstellung von MEMS-Bauelementen werden meist die aus der Halbleitertechnik bekannten Materialien und Prozesse benutzt. Als Materialien kommen Silicium, Polymere, Metalle oder Keramiken zum Einsatz. Auf diesen Materialien werden durch Gasphasenabscheidung die benötigten Materialschichten mit einer Schichtdicke zwischen einigen 10 Nanometern bis etwa 100 Mikrometer aufgebracht. In diesen Materialschichten werden durch unterschiedliche Lithografieverfahren zunächst die benötigten feinen Strukturen angelegt, die danach mit Hilfe von Ätzverfahren in die Materialschichten eingeätzt werden.[3] Hierbei kommen insbesondere die Ätzverfahren zur Anwendung, die zu einem großen Aspektverhältnis der geätzten Gräben führen.
Materialien[Bearbeiten | Quelltext bearbeiten]
Silicium[Bearbeiten | Quelltext bearbeiten]
Hochreines kristallines Silicium ist das Grundmaterial für die meisten Halbleiter-Bauelemente in der Mikroelektronik. Silicium und seine Verbindungen (Siliciumdioxid, Siliciumnitrid usw.) ist hinsichtlich seiner Verfügbarkeit und seiner chemischen, physikalischen und anderen technisch nutzbaren Eigenschaften dafür am besten geeignet. Auch für die meisten Mikro-Elektromechanischen Systeme ist Silicium das am besten geeignete Grundmaterial.
Durch die mechanischen Materialeigenschaften des kristallinen Siliciums ist Silicium ein fast perfektes Hookesches Material mit linear-elastischem Verhalten ohne nennenswerte Hysterese, wodurch mechanische Verformungen nahezu ohne Energieverlust möglich sind. Außerdem zeichnet sich Silicium durch eine sehr große Beständigkeit gegenüber Vibrationen und Schwingungen mit sehr geringer Materialermüdung aus, wodurch eine sehr große Service-Lebensdauer ohne die Gefahr eines Bruches erreicht werden kann.
Polymere[Bearbeiten | Quelltext bearbeiten]
Obwohl kristallines Silicium in der Elektronik in großen Mengen benötigt wird und mit großer Wirtschaftlichkeit hergestellt wird, ist es immer noch ein komplexes und relativ teures Material. Polymere hingegen können in riesigen Volumina mit einer Vielzahl von Materialeigenschaften hergestellt werden. Spezielle MEMS-Bauelemente werden deshalb auch aus Polymeren nach Verfahren wie Spritzguss, Prägung oder Stereolithographie hergestellt. Sie eignen sich besonders gut für mikrofluidische Anwendungen wie in Geräten zur Einweg-Blutprobe.
Metalle[Bearbeiten | Quelltext bearbeiten]
Einige spezielle MEMS-Bauelemente werden auch aus oder mit Metall hergestellt. Obwohl Metalle keine der Vorteile gegenüber Silicium in Bezug auf die mechanischen Eigenschaften haben, können sie neben hoher Zuverlässigkeit Eigenschaften aufweisen, wie sie beispielsweise in Katalysatoren benötigt werden. Metalle können durch Galvanisierung, Verdampfung oder Sputtern in den MEMS-Bauelementen abgelagert werden. Häufig verwendete Metalle sind Gold, Nickel, Aluminium, Kupfer, Chrom, Titan, Wolfram, Platin und Silber.
Keramiken[Bearbeiten | Quelltext bearbeiten]
In MEMS-Bauelementen weisen Nitride aus Silicium, Aluminium und Titan sowie Siliciumcarbid und andere Keramiken vorteilhafte Materialeigenschaften auf die zunehmend genutzt werden. Aluminiumnitrid (AlN) beispielsweise kristallisiert in der Wurtzitstruktur und hat pyroelektrische und piezoelektrische Eigenschaften. Damit werden Sensoren hergestellt, die auf Normal- und Scherkräfte reagieren.[4] Titannitrid (TiN) weist dagegen eine hohe elektrische Leitfähigkeit und einen großen Elastizitätsmodul auf, wodurch elektrostatische MEMS-Bauelemente mit ultradünnen Membranen realisiert werden können.[5] Darüber hinaus qualifiziert die hohe Beständigkeit von TiN gegen Biokorrosion das Material für Anwendungen in Biosensoren.
Abscheidungsprozesse[Bearbeiten | Quelltext bearbeiten]
Physikalische Gasphasenabscheidung[Bearbeiten | Quelltext bearbeiten]
Mit dem Begriff physikalische Gasphasenabscheidung (PVD) wird eine Gruppe von vakuumbasierten Beschichtungsverfahren bzw. Dünnschichttechnologien bezeichnet, bei denen mithilfe physikalischer Verfahren das Ausgangsmaterial in die Gasphase überführt wird und das gasförmige Material anschließend zum zu beschichtenden Substrat geführt wird, wo es kondensiert und die Zielschicht bildet. Zu diesen Techniken gehören das Verfahren des Sputterns, bei dem ein Ionenstrahl Atome aus einem Target freisetzt, die sich anschließend auf dem gewünschten Substrat ablagern. Weiterhin werden unterschiedliche Verdampfungsverfahren eingesetzt, beispielsweise Thermisches Verdampfen, Elektronenstrahlverdampfen oder Laserstrahlverdampfen, bei denen ebenfalls dünne Schichten auf einem Substrat abgeschieden werden können.
Chemische Gasphasenabscheidung[Bearbeiten | Quelltext bearbeiten]
Mit dem Begriff chemische Gasphasenabscheidung (CVD) werden verschiedene Beschichtungsverfahren bezeichnet, bei denen an der erhitzten Oberfläche eines Substrates aufgrund einer chemischen Reaktion aus der Gasphase eine dünne Schicht eines Feststoffes abgeschieden wird. Voraussetzung hierfür ist, dass flüchtige Verbindungen der abzuscheidenden Schicht existieren, die bei einer bestimmten Reaktionstemperatur die feste Schicht abscheiden. Die Varianten der chemischen Abscheidetechniken unterscheiden sich durch unterschiedliche Temperaturen und Arbeitsdrücke. Oxidschichten auf einem Substrat (Wafer) können auch durch thermische Oxidation gebildet werden [typischerweise auf Silizium), wobei das Substrat dem Sauerstoff ausgesetzt wird, um eine dünne Oberflächenschicht aus Siliciumdioxid zu erzeugen.
Strukturierung[Bearbeiten | Quelltext bearbeiten]
Fotolithografie[Bearbeiten | Quelltext bearbeiten]
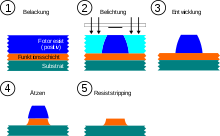
Die Fotolithografie ist das am häufigsten verwendete Verfahren zur Herstellung von Strukturen zur Herstellung von MEMS-Bauelementen. Sie wird typischerweise bei Dünnschichtabscheidungen im Zusammenhang mit Nass- und Trockenätzverfahren verwendet. In der Regel kommt die anspruchsvolle Immersionslithografie zur schärferen Abbildungen der Strukturen zur Anwendung. Dabei wird das Muster in ein lichtempfindliches Material durch selektive Belichtung, z. B. durch Maskieren eines Teils der Strahlung, mit einer Strahlungsquelle auf ein lichtempfindliches Material übertragen. Der belichtete Bereich, dessen chemische Eigenschaften sich vom unbelichteten Bereich unterscheiden, kann dann chemisch entfernt oder behandelt werden.
Elektronenstrahllithografie[Bearbeiten | Quelltext bearbeiten]

Die Elektronenstrahllithografie (ESL) ist in der Mikro- und Halbleitertechnik ein spezielles Verfahren zur Strukturierung einer Elektronenstrahl-empfindlichen Schicht (resist) Das Verfahren gehört zur Gruppe der Next-Generation-Lithografie. Durch die „Belichtung“ mit einem Elektronenstrahl wird der Resist chemisch geändert, so dass er lokal gelöst werden kann (Entwicklung) und eine strukturierte Resistschicht entsteht. Die Struktur kann anschließend auf eine Schicht aus einem anderen Material übertragen werden, z. B. durch Ätzen einer darunterliegenden Schicht oder durch selektive Abscheidung eines Materials auf dem Resist. Der wesentliche Vorteil der Elektronenstrahllithografie ist, dass Strukturen mit deutlich geringeren Abmessungen (≤50 nm) als bei der Fotolithografie hergestellt werden können. Der Nachteil der Elektronenstrahllithographie ist die recht lange Zeit, die benötigt wird, um bei diesem Verfahren ein vollständiges Silicium-Wafer- oder Glassubstrat belichten zu können.
Ionenstrahllithografie[Bearbeiten | Quelltext bearbeiten]
Die Ionenstrahllithografie (ISL) ist eng verwandt mit der Elektronenstrahllithografie und führt ebenfalls zu Strukturen in der Größenordnung „nm“. Der wesentliche Vorteil der Ionenstrahllithografie liegt in der geringeren Streuung der Ionen gegenüber der Elektronenstrahllithografie wodurch kleinere Strukturen realisierbar sind. Allerdings besteht eine maximale Tiefe bis zu der die Ionen in das Substrat/die Schicht eindringen, sie liegt für Ionen mit Energien unterhalb von 1 MeV bei maximal 500 nm. Daher können nur sehr dünne Schichten strukturiert werden.
Ionenspurtechnologie[Bearbeiten | Quelltext bearbeiten]

Die Ionenspurtechnologie ist die Anwendung von Ionenspuren in Mikro- und Nanotechnologie.[6] Die Auflösungsgrenze liegt bei etwa 8 nm für strahlungsresistente Mineralien, Gläser und Polymere. Dieses Verfahren ist in der Lage, Löcher oder Schnitte ohne einen zusätzlichen Entwicklungsprozess in dünnen Schichten zu erzeugen. Die Strukturtiefe kann entweder durch den Ionenbereich oder durch die Materialdicke der Schicht definiert werden. Es können Aspektverhältnisse (das Verhältnis aus der Tiefe bzw. Höhe einer Struktur zu ihrer kleinsten lateralen Ausdehnung) von bis zu mehreren 10.000 erreicht werden. Geätzte Spurzylinder können als Filter [7][8] oder als Zählöffnungen genutzt werden.[9] Sie können durch Monolagen verändert werden,[10] oder durch elektrochemische Abscheidung gefüllt werden.[11][12] Diese Technik kann außerdem Formen in einem definierten Neigungswinkel bilden.
Röntgenlithografie[Bearbeiten | Quelltext bearbeiten]
Die Röntgenlithographie ist ein Strukturierungsverfahren, das verwendet wird, um selektiv Teile einer dünnen Schicht zu entfernen. Es verwendet Röntgenstrahlen, um ein geometrisches Muster von einer Maske in eine Photoresist-Dünnschicht zu übertragen die sich auf einem Wafer befindet. Dieses Muster kann anschließend durch weitere Verfahren in das darunterliegende Material übertragen oder für die selektive Abscheidung von Material genutzt werden.
Mechanische Abformung (LIGA)[Bearbeiten | Quelltext bearbeiten]
Das deutsche Akronym LIGA steht für die Verfahrensschritte: Lithographie, Galvanik und Abformung und bezeichnet ein Verfahren, welches auf einer Kombination von Fotolithographie, Galvanik und Mikroabformung basiert. Mit diesem Verfahren wird ein Substrat zunächst mit einem Metall beschichtet, das dann anschließend mittels Fotolithografie und Ätzung in eine mechanische Negativform gebracht wird. Mit Hilfe dieser Negativform wird dann ein metallischer oder keramischer Mikro-Stempel erzeigt, der zur Formgebung (Abformung) einer Mikrostruktur verwendet werden kann. Das Verfahren ermöglicht die Herstellung von Mikrostrukturen mit kleinsten Abmessungen bis zu 0,2 µm, Strukturhöhen bis 3 mm, und Aspektverhältnissen bis 50 (für Detailstrukturen bis 500) aus den Materialien Kunststoff, Metall oder Keramik.[13]
Das LIGA-Verfahren wurde Anfang der 1980er Jahre am damaligen Kernforschungszentrum Karlsruhe von einem Team unter Leitung von Erwin Willy Becker und Wolfgang Ehrfeld im Rahmen der Entwicklung des Trenndüsenverfahrens zur Urananreicherung entwickelt, um extrem kleine Trenndüsen herstellen zu können.
Ätzen[Bearbeiten | Quelltext bearbeiten]
- Trennschärfe und Richtungsabhängigkeit von Ätzverfahren
-
Trennschärfe: Ein Ätzverfahren mit geringer Trennschärfe attackiert auch das Trägermaterial (1), Ein Ätzverfahren mit großer Trennschärfe lässt das Trägermaterial unbeeinflusst (2).
-
Richtungsabhängigkeit: Ein perfekt isotropisches Ätzverfahren ist ungerichtet und hinterlässt abgerundete Seitenwände (1). Ein perfekt anisotropisches Ätzverfahren führt zu vertikalen Seitenwänden (2).
Prozessbeschreibung[Bearbeiten | Quelltext bearbeiten]
Aspektverhältnis (Tiefe:Breite) | bis 50:1 |
Flankenwinkel | 90° ± 2° |
Ätzrate | (max.)20 µm/min (standard) 1–2 µm/min |
Oberflächenrauhigkeit | 10 nm |

Der DRIE-Prozess ist wie der ursprüngliche Bosch-Prozess ein zweistufiger, alternierender Trockenätzprozess, bei dem sich Ätz- und Passivierungsschritte abwechseln. Ziel ist es, möglichst anisotrop zu ätzen, das heißt richtungsabhängig, senkrecht zur Wafer-Oberfläche. Auf diese Weise können beispielsweise sehr schmale Gräben geätzt werden.
Die Prozesse lassen sich wie folgt zusammenfassen. Zunächst wird der Silicium-Wafer maskiert, beispielsweise mit Fotolack oder mit einer Hartmaske aus Siliciumdioxid, Siliciumnitrid und anderen Stoffen, die jene Stellen des Wafers abdeckt, die nicht geätzt werden sollen. Anschließend beginnt der eigentliche Ätzprozess. Dazu wird Schwefelhexafluorid (SF6) in einem Trägergas (meist Argon) in den Reaktor mit dem darin befindlichen Substrat eingeleitet. Durch Erzeugen eines energiereichen Hochfrequenzplasmas entsteht aus dem SF6 ein reaktives Gas. Zusammen mit der Beschleunigung der Ionen in einem elektrischen Feld wird eine chemische isotrope Ätzreaktion durch aus SF6 gebildete Radikale und ein physikalischer anisotroper Materialabtrag durch Sputtern mittels Argon-Ionen überlagert.
Der Ätzprozess wird nach kurzer Zeit gestoppt und ein Gasgemisch aus Octafluorcyclobutan (C4F8) und Argon als Trägergas eingeleitet; auch andere Gasgemische sind möglich, beispielsweise CF4/H2. Im Plasma des Reaktors wird Octafluorcyclobutan aktiviert und bildet auf dem gesamten Substrat eine Polymer-Passivierungsschicht, das heißt sowohl auf der Maske als auch auf dem Boden und den vertikalen Seitenwänden des Grabens/Lochs. Auf diese Weise werden die Seitenwände im Folgenden vor weiterem chemischen Materialabtrag geschützt, um die Anisotropie des Gesamtprozesses zu gewährleisten. Denn durch den anschließend wiederholten Ätzschritt mit SF6 wird die Passivierungsschicht der horizontalen Flächen (Grabenboden) durch die gerichtete physikalische Komponente (Ionen) der Ätzreaktion deutlich schneller entfernt als die Schicht an den Seitenwänden.
Beide Schritte werden nun so lange wiederholt, bis die gewünschte Bearbeitungstiefe erreicht ist. Wichtig ist dabei die Balance zwischen dem Ätz- und Passivierungsschritt. Wird beispielsweise die Polymerschicht zu dick aufgetragen, wird ein Großteil des Ätzgases und der Prozesszeit für den Abtrag des Polymers am Grabenboden verwendet, was zu höheren Prozesskosten führt. Wird die Schicht jedoch zu dünn aufgetragen oder ist das elektrische Feld für den Ionentransport zum Substrat zu gering gewählt, werden die Seitenwände zu stark geätzt.
Die Prozessparameter haben auch entscheidenden Einfluss auf die Struktur der Seitenwände; diese sind aufgrund des alternierenden Prozessablaufs in der Regel nicht glatt, sondern leicht gewellt. Die Stärke der Wellen kann jedoch durch geeignete Wahl der Prozessparameter minimiert werden, so dass sie die nachfolgenden Prozesse in der Herstellung nicht negativ beeinflusst.
Nach dem Ätzen müssen abschließend das Maskenmaterial (das ebenfalls teilweise geätzt wird) und die Passivierungschicht an den Grabenwänden entfernt werden.
Ein Nachteil des Verfahrens sind die im Vergleich zum Nassätzen sehr hohen Anlagenkosten sowie der geringe Fertigungsdurchsatz.
Neben dem alternierenden Prozess gibt es auch das Verfahren des gleichzeitigen Ätzens und Passivierens, ein sogenannter kontinuierlicher Prozess.
MEMS-Bauelemente[Bearbeiten | Quelltext bearbeiten]
Sensoren[Bearbeiten | Quelltext bearbeiten]
Beschleunigungssensoren[Bearbeiten | Quelltext bearbeiten]
Drehratensensoren[Bearbeiten | Quelltext bearbeiten]
Drucksensoren[Bearbeiten | Quelltext bearbeiten]
Mikrobolometer (Strahlungssensor)[Bearbeiten | Quelltext bearbeiten]
Pyroelektrische Sensoren[Bearbeiten | Quelltext bearbeiten]
Mikrofluidik[Bearbeiten | Quelltext bearbeiten]
Microdispenser[Bearbeiten | Quelltext bearbeiten]
Microfluidiks für In vitro diagnostics[Bearbeiten | Quelltext bearbeiten]
Microfluidics for Research[Bearbeiten | Quelltext bearbeiten]
Druckerköpfe[Bearbeiten | Quelltext bearbeiten]
Optische Aktuatoren[Bearbeiten | Quelltext bearbeiten]
Optische Schalter[Bearbeiten | Quelltext bearbeiten]
Projektions-Systeme (Mikrospiegelaktor)[Bearbeiten | Quelltext bearbeiten]
Interferometric modulator display (digitale Displays)[Bearbeiten | Quelltext bearbeiten]
Weitere Anwendungen[Bearbeiten | Quelltext bearbeiten]
Oszillatoren[Bearbeiten | Quelltext bearbeiten]
RF MEMS[Bearbeiten | Quelltext bearbeiten]
Inertial Combos[Bearbeiten | Quelltext bearbeiten]
Automatic Test Equipment (ATE)[Bearbeiten | Quelltext bearbeiten]
Mikrofone[Bearbeiten | Quelltext bearbeiten]
Ultraschallwandler[Bearbeiten | Quelltext bearbeiten]
Digitaler Kompass[Bearbeiten | Quelltext bearbeiten]
Markt[Bearbeiten | Quelltext bearbeiten]
References[Bearbeiten | Quelltext bearbeiten]
- ↑ TU-Muenchen [[1]]
- ↑ Jeffrey Funk, Sensors, MEMS, Internet of Things, Workshop May 2012 [2]
- ↑ R. Ghodssi, P. Lin: MEMS Materials and Processes Handbook. Springer, 2011, ISBN 978-0-387-47316-1.
- ↑ T. Polster, M. Hoffmann: Aluminium nitride based 3D, piezoelectric, tactile sensors. In: Proc. Chem. 1. Jahrgang, 2009, S. 144–7, doi:10.1016/j.proche.2009.07.036.
- ↑ M. Birkholz, K.-E. Ehwald, P. Kulse, J. Drews, M. Fröhlich, U. Haak, M. Kaynak, E. Matthus, K. Schulz: Ultrathin TiN membranes as a technology platform for CMOS-integrated MEMS and BioMEMS devices. In: Adv. Func. Mat. 21. Jahrgang, Nr. 9, 2011, S. 1652–1654, doi:10.1002/adfm.201002062 (researchgate.net [PDF]).
- ↑ R. Spohr: Ion tracks and microtechnology. Vieweg Verlag, 1990, ISBN 3-528-06330-0 (ion-tracks.de).
- ↑ R.L. Fleischer, P.B. Price and R.M. Walker: Method of forming fine holes of near atomic dimensions. In: Review of Scientific Instruments. 34. Jahrgang, Nr. 5, 1963, S. 510–512, doi:10.1063/1.1718419, bibcode:1963RScI...34..510F.
- ↑ P. Apel: Swift ion effects in polymers: industrial applications. In: Nuclear Instruments and Methods in Physics Research Section B. 208. Jahrgang, 2003, S. 11–20, doi:10.1016/S0168-583X(03)00634-7, bibcode:2003NIMPB.208...11A.
- ↑ R.W. DeBlois, C.P. Bean: Counting and sizing of submicron particles by the resistive pulse technique. In: Review of Scientific Instruments. 41. Jahrgang, Nr. 7, 1970, S. 909–916, doi:10.1063/1.1684724, bibcode:1970RScI...41..909D.
- ↑ W.J. Petzny, J.A. Quinn: Calibrated membranes with coated pore walls. In: Science. 166. Jahrgang, Nr. 3906, 1969, S. 751–753, doi:10.1126/science.166.3906.751, bibcode:1969Sci...166..751P.
- ↑ G.E. Possin: A method for forming very small diameter wires. In: Review of Scientific Instruments. 41. Jahrgang, Nr. 5, 1970, S. 772–774, doi:10.1063/1.1684640, bibcode:1970RScI...41..772P.
- ↑ J. Vetter: Freistehende Metallwhisker. GSI Darmstadt, abgerufen am 27. April 2010.
- ↑ E. W. Becker, W. Ehrfeld, P. Hagmann, A. Maner, D. Münchmeyer: Fabrication of microstructures with high aspect ratios and great structural heights by synchrotron radiation lithography, galvanoforming, and plastic moulding (LIGA process). In: Microelectronic Engineering. Band 4, Nr. 1, 1986, S. 35–56, doi:10.1016/0167-9317(86)90004-3.