Benutzer:Krizu/Werkstatt
Das maschinelle Oberflächenhämmern (engl. machine hammer peening, MHP, auch: Festklopfen, Klopfen, Schlagverdichten) ist ein Fertigungsverfahren zur mechanischen Oberflächenbehandlung von Metallwerkstoffen. Durch hochfrequente Schläge eines Hammerwerkzeugs kommt es sowohl zu einer Oberflächeneinglättung als auch zu einer Induktion von Kaltverfestigung und Druckeigenspannungen. Das MHP hat seinen industriellen Ursprung im Werkzeug- und Formenbau zur Oberflächenglättung von Ziehwerkzeugen der Automobilindustrie,[1] wird aber mittlerweile sehr vielfältig eingesetzt.


Der englischsprachige Begriff Pneumatic Impact Treatment (PIT) bezeichnet ein Nachbehandlungsverfahren, wobei durch höherfrequentes Hämmern der Oberfläche eine Steigerung der Ermüdungsfestigkeit erzielt wird. Im Speziellen wird die Methode bei Schweißverbindungen angewendet, wobei eine wesentliche Erhöhung der Lebensdauer erreicht werden kann. Die Wirkungsweise beruht dabei auf einer Reduktion der geometrischen Kerbwirkung am Nahtübergang, einem Aufbau von Druckeigenspannungen und einer Verfestigung des Materials im nachbehandelten Bereich. Durch die einfache Bedienbarkeit und einer hohen Reproduzierbarkeit zeichnet sich das Verfahren insbesondere für industrielle Anwendungen im Anlagen-, Behälter-, Maschinen- oder Stahlbau aus.

Der englischsprachige Begriff High Frequency Impact Treatment, abgekürzt als HiFIT-Verfahren und im Deutschen Hochfrequentes Hämmerverfahren bzw. Hochfrequenzhämmern genannt, bezeichnet die Nachbehandlung geschweißter Stahlkonstruktionen am Schweißnahtübergang zur Steigerung der Ermüdungsfestigkeit.
Ermüdungsfestigkeit[Bearbeiten | Quelltext bearbeiten]
Unter Materialermüdung wird eine Schädigung oder ein Versagen von Bauteilen und Werkstoffen unter zyklischer Beanspruchung verstanden. Es bilden sich dabei Anrisse bevorzugt an Kerben, Fehlstellen oder hochbeanspruchten Zonen, welche sich fortlaufend vergrößern und schließlich zum Versagen oder Ausfall der Komponente führen.[2] Im Allgemeinen steigt die Ermüdungsfestigkeit mit zunehmender statischer Festigkeit eines Werkstoffs. Im Fall von geometrischen Unregelmäßigkeiten wie Kerben, welche konstruktionsbedingt oder durch Schweißverbindungen entstehen können, ist dieser Zusammenhang durch die zunehmende Kerbempfindlichkeit hochfester Materialien, nur bedingt erfüllt. Aus diesem Grund ist das Ermüdungsverhalten geschweißter Stahlverbindungen nach aktuellen Richtlinien [3] und Empfehlungen [4][5] generell unabhängig von der Streckgrenze des verwendeten Grundmaterials. Bedingt durch die ständig wachsenden Forderungen nach einer erhöhten Leichtbauweise und einer Steigerung der Lebensdauer von Komponenten und Strukturen, ist jedoch eine Verbesserung des Ermüdungsfestigkeitsverhaltens unerlässlich. Dies kann beispielsweise durch den Einsatz einer PIT-Nachbehandlung bei höher- und hochfesten, aber auch niederfesten Grundmaterialien erzielt werden.
Verfahrensbeschreibung[Bearbeiten | Quelltext bearbeiten]
Das PIT-Verfahren ist ein pneumatisch betriebenes, höherfrequentes Hämmerverfahren, welches zur mechanischen Nachbehandlung von geschweißten Verbindungen und hochbeanspruchten ungeschweißten Zonen eines Bauteils entwickelt wurde. Sowohl die Bearbeitungsfrequenz, als auch die Schlagintensität sind unabhängig voneinander einstellbar, wodurch es möglich ist den unterschiedlichen Anforderungen verschiedener Werkstoffe und Schweißnahtgeometrien gerecht zu werden. Ein pneumatischer Muskel im Gerät wandelt die Druckenergie in mechanische Impulse um, die durch einen oder mehrere gehärtete Stahlbolzen auf die zu behandelnde Oberfläche übertragen werden. Um die Vibrationen während der Behandlung möglichst gering zu halten, ist ein weiteres Federsystem inkludiert, so dass das Handgerät von der Schlagkraft vollständig entkoppelt ist. Dies bewirkt eine geringe Handarmvibration in der Höhe von rund 5 m/sek für den Bediener und zusätzlich ergibt sich eine nahezu konstante Schlagkraft, wodurch eine hohe Reproduzierbarkeit gewährleistet ist. Die Vorschubgeschwindigkeit bei Stahl beträgt etwa 20 cm/min bei einer frei wählbaren Bearbeitungsfrequenz des oder der Stahlbolzen von bis zu 80 bis 120 Hz. Über die Druckluft lässt sich die Schlagintensität stufenlos einstellen, wobei im Gegensatz zu anderen Verfahren das Gerät bereits bei einem Druck von unter 4 bis 5 bar funktionstüchtig ist und somit einen geringen Luftverbrauch von etwa 175 bis 250 l/min aufweist. Das Abführen der Abluft nach vorne zur Bearbeitungsstelle hat den Vorteil, dass Lackpartikel, Metallspäne und sonstige Verunreinigungen weggeblasen und nicht ungewollt in die Werkstückoberfläche eingedrückt werden, und die strömende Luft den oder die Bolzen kühlt und dadurch die Standzeit deutlich erhöht wird.[6]
Wirkungsweise[Bearbeiten | Quelltext bearbeiten]
Gegenüber anderen Nachbehandlungsverfahren, wie zum Beispiel Schleifen, Kugelstrahlen oder Spannungsarmglühen, wobei eine Steigerung der Ermüdungsfestigkeit bzw. Lebensdauer meist nur durch einen Effekt erzielt wird, kommen beim PIT-Verfahren folgende Wirkungsweisen kombiniert zur Geltung:
Reduktion der geometrischen Kerbwirkung[Bearbeiten | Quelltext bearbeiten]
Durch die Nachbehandlung wird der für die Ermüdungsbeanspruchung kritische Übergang vom Grundmaterial zur Schweißnaht ausgerundet, wodurch dies zu einer wesentlichen Reduzierung der geometrischen Kerbwirkung in diesem Bereich führt. Speziell bei kerbscharfen Geometrien, wie zum Beispiel Schweißnahtenden, trägt dieser Effekt wesentlich zur Wirkungsweise bei.
Verfestigung des Materials[Bearbeiten | Quelltext bearbeiten]
Bedingt durch die Umformung des Materials findet im nachbehandelten Bereich eine lokale Verfestigung statt. Je nach Werkstoff und Verfestigungsverhalten kann dies zu einer wesentlichen Erhöhung der Härte und somit auch zu einer Festigkeitssteigerung führen.
Aufbau von Druckeigenspannungen[Bearbeiten | Quelltext bearbeiten]
Zusätzlich zur lokalen Verfestigung werden Druckeigenspannungen eingebracht, welche entgegen den ermüdungsrelevanten Zugspannungen wirken und dadurch die gesamte Beanspruchung in der höchstbelasteten Zone senken. Zur Verifikation des sich ausbildenden Eigenspannungszustandes durch die Nachbehandlung können Messungen der Eigenspannungen mittels Röntgendiffraktometrie oder Bohrlochmethode dienen, aber auch eine Abschätzung des lokalen Eigenspannungszustandes basierend auf einer numerischen Simulation ist möglich.
Forschungsergebnisse[Bearbeiten | Quelltext bearbeiten]
Im Rahmen des International Institute of Welding (IIW) wurde der Effekt von Schweißnahtnachbehandlungen auf die Ermüdungsfestigkeit bereits umfassend untersucht, woraus auch internationale Empfehlungen[4] und Anwendungsrichtlinien[5] entstanden sind. Das höherfrequente Hämmern wurde hierbei unter dem englischen Begriff High Frequency Mechanical Impact (HFMI) Treatment eingeführt und basierend auf aktuellen Forschungsergebnissen wurden Vorschläge für eine von der Grundmaterialfestigkeit abhängige Steigerung der Ermüdungsfestigkeit ausgearbeitet, welche derzeit in die Richtlinien eingefügt werden.[7][8][9] Zahlreiche Untersuchungsergebnisse[10][11][12] für geschweißte Stahlverbindungen mit einer Streckgrenze von 235 bis 1300 MPa zeigen beispielhaft, dass durch eine PIT-Nachbehandlung eine wesentliche Steigerung der Ermüdungsfestigkeit von bis zu 250 % im Bereich der Langzeitfestigkeit (ab rund einer Millionen Lastzyklen) erreicht werden kann. Durch vergleichende Versuche an Grundmaterialproben wird außerdem verdeutlicht, dass bei einer Anwendung des Verfahrens die Ermüdungsfestigkeit des Grundmaterials nahezu zur Gänze ausgenutzt werden kann, womit ein hohes Leichtbaupotential für geschweißte Strukturen gegeben ist. Des Weiteren wird gezeigt, dass diese Nachbehandlungstechnik eine effektive Möglichkeit zur Ertüchtigung bereits bestehender Strukturen darstellt.[13]
Qualitätssicherung[Bearbeiten | Quelltext bearbeiten]
Zur industriellen Anwendung ist eine hohe Reproduzierbarkeit und qualitätssichernde Maßnahmen ein wesentlicher Aspekt. Neben einer fachlich fundierten Einschulung und Sensibilisierung des Bedieners kann die Qualität einerseits durch optische Kontrollen der Behandlungsspur nach der Anwendung, sowie durch eine Prüfung der Intensität der Behandlung mit Hilfe des PIT-ALMEN Intensitätstests vor der Nachbehandlung erfolgen. Durch diese Maßnahmen wird eine gleichbleibende Qualität und Wirkung des PIT-Verfahrens nachhaltig gewährleistet.[14]
Vorteile durch PIT[Bearbeiten | Quelltext bearbeiten]
Der wesentliche Vorteil durch die PIT-Behandlung besteht in einer Steigerung der Ermüdungsfestigkeit und in weiterer Folge der Lebensdauer geschweißter Verbindungen und hochbeanspruchter Komponenten. Durch das Verfahren kann einerseits die Festigkeit nieder-, höher- und hochfester Grundmaterialien nahezu zur Gänze ausgenutzt werden, wodurch ein erhebliches Leichtbaupotential und eine Einsparung von Kraftstoffverbrauch und Schadstoffemission entsteht, aber auch eine Ertüchtigung von Bauteilen im Betrieb ist wirkungsvoll möglich. Die kompakte und äußerst transportable PIT-Anlage ermöglicht auch eine problemlose Behandlung von Schweißnähten auf Baustellen. Durch den speziellen mechanischen Aufbau ist es möglich die Anlage in einen automatisierten Herstellprozess zu integrieren, zum Beispiel als Aufbau an einem Roboter, welcher bei großen Stückzahlen und langen Schweißnähten effizient einsetzbar ist. Generell bietet das PIT-Verfahren folgende Vorteile, welche durch zahlreiche Untersuchungen in Wissenschaft und Industrie bestätigt wurden:[15][16][17]
- Erhöhung der Lebensdauer
- Steigerung des Leichtbaupotentials
- Verminderung und Kontrolle des Schweißverzugs
- Ertüchtigung vorgeschädigter Schweißverbindungen
- Erhöhung der Oberflächenhärte
- Verbesserung des Spannungsrisskorrosionswiderstands
Anwendungsbeispiele[Bearbeiten | Quelltext bearbeiten]
Das PIT-Verfahren wird bereits vielfach im industriellen Sektor eingesetzt, wobei nachfolgend ausgewählte Anwendungsbeispiele vorgestellt werden.[18]
Anlagen- und Stahlbau: Tragwerke und Stahlwasserbau[Bearbeiten | Quelltext bearbeiten]
Insbesondere im Bereich des Bauwesens ist eine ermüdungsgerechte Konstruktion und Auslegung für einen sicheren Betrieb über die gesamte Lebensdauer wesentlich. Basierend auf den guten Erfahrungen beim Neubau von Straßenbrücken wurde das PIT-Verfahren auch zur Nachbehandlung geschweißter Fahrbahnübergangskonstruktionen aus Baustahl eingesetzt. Begleitende Versuche an Strukturkomponenten bestätigen die effektive Wirkung der Methodik und bilden die Grundlage für eine nachfolgende Anwendungszulassung.[19]

Weitere Untersuchungen an Referenzproben mit strukturellen Details des Stahlwasserbaus zeigen, dass die Technologie auch für eine Instandhaltung bereits vorgeschädigter Bauteile besonders wirkungsvoll und für lebensdauerverlängernde Maßnahmen in diesem Bereich anzuwenden ist.[20]
Behälterbau: Kernfusionsreaktor[Bearbeiten | Quelltext bearbeiten]
Zur Kontrolle des Verzugs beim Einschweißen von Rohrstutzen in die vorhandene Behälterkonstruktion eines Reaktors muss die Wärmeeinbringung beim Schweißprozess so gering wie möglich gehalten werden, wodurch eine zusätzliche Kühlung mit Trockeneis notwendig ist. Durch eine PIT-Nachbehandlung jeder Schweißlage können die durch den Fügeprozess bedingten Zugeigenspannungen klein gehalten werden, wobei ein praktisch verzugsfreies Schweißen ermöglicht und der Aufwand durch nachfolgende Bearbeitungsschritte minimiert wird.[21]
Maschinenbau: Leichtbaupotential[Bearbeiten | Quelltext bearbeiten]
Im Bereich des Maschinenbaus wird das Verfahren in Kombination mit nieder-, höher- und hochfesten Stählen vielfach zur Steigerung des Leichtbaupotentials angewendet. Beispielsweise bei Kränen und kranähnlichen Strukturen kann durch diese Vorgehensweise eine wesentliche Gewichtseinsparung bei gleichbleibender Kranreichweite erzielt werden, wodurch ein Treibstoff- und Schadstoffreduzierender Betrieb bei höherer Lebensdauer möglich ist.[12]
Eigenschaften[Bearbeiten | Quelltext bearbeiten]

Die Betriebsfestigkeit und Lebensdauer dynamisch belasteter, geschweißter Stahlkonstruktionen wird in vielen Fällen durch die Schweißnähte, insbesondere die Schweißnahtübergänge bestimmt. Durch gezielte Nachbehandlung der Übergänge (Schleifen, Strahlen, Hämmern etc.) kann die Lebensdauer mit einfachen Mitteln bei vielen Konstruktionen erheblich gesteigert werden. Hämmerverfahren haben sich dabei als besonders effiziente Nachbehandlungsmethoden erwiesen und wurden im Rahmen des Verbundprojektes REFRESH[22] ausführlich untersucht und weiterentwickelt. Das HiFIT-Verfahren ist ein solches Hämmerverfahren, das universell einsetzbar ist, nur einen geringen gerätetechnischen Aufwand erfordert und dennoch eine hohe Reproduzierbarkeit und die Möglichkeit zur Qualitätsüberwachung bietet.
Wirkungsweise[Bearbeiten | Quelltext bearbeiten]

Der HiFIT-Hammer arbeitet mit einem gehärteten Pin mit einer gerundeten Spitze mit einem Durchmesser von 3 mm. Dieser Pin wird mit einer einstellbaren Intensität und einer Frequenz von 150...300 Hz auf den Übergangsbereich von der Schweißnaht zum Grundwerkstoff gehämmert. Es entstehen lokale Umformungen in Form einer Nachbehandlungsspur.
Im Wesentlichen basiert der Erfolg einer HiFIT-Behandlung auf den folgenden Wirkungsweisen:
1. Reduzierung der Kerbwirkung durch Umformung bzw. Ausrundung des Nahtübergangs und Entfernen von Schweißnahtfehlern.
2. Verfestigung der Randschicht zur Erhöhung des Widerstandes gegen Rissbildung und Rissausbreitung.
3. Einbringen von Druckeigenspannungen zur Erhöhung des Widerstandes gegen Rissbildung und Rissausbreitung durch Überlagerung der Kerbspannungen mit Druckeigenspannungen.
Varianten[Bearbeiten | Quelltext bearbeiten]
Um die Zugänglichkeit zur Nachbehandlungsstelle zu verbessern, sowie zur Ausrundung von Bauteil-Innenkanten ohne Schweißungen, gibt es zahlreiche Varianten von Spezialpins in verschiedenen Durchmessern und Längen. Zur Behandlung von speziellen Werkstoffen werden Pin-Varianten aus „verträglichen“ Werkstoffen bereitgestellt. Sondervarianten für Spezialanwendungen sind auf Kundenwunsch häufig im Einsatz.
Nachweise[Bearbeiten | Quelltext bearbeiten]
Das Internationale Institut für Schweißtechnik IIW veröffentlichte im Oktober 2016 die Richtlinie „IIW Recommendations for the HFMI Treatment“. Es wird ein Überblick von höherfrequenten Hämmermethoden (HFMI) präsentiert. Darüber hinaus werden Empfehlungen zur korrekten Anwendung des Verfahrens und zu quantitativen Messungen zur Qualitätssicherung beschrieben. Die Richtlinie stellt Bemessungsgrundlagen von HFMI-verbesserten Schweißverbindungen, auf der Basis von Nennspannungs-, Strukturspannungs- und Kerbspannungskonzepten vor.
Im Forschungsprojekt „REFRESH - Lebensdauerverlängerung bestehender und neuer geschweißter Stahlkonstruktionen“ (P702)[22] von 2006–2009 konnte in zahlreichen Versuchsreihen eine 80- bis 100-prozentige Steigerung der Schweißnahtermüdungsfestigkeit und eine 5- bis 15-fache Erhöhung der Schweißnahtlebensdauer nachgewiesen werden. Im Rahmen dieses Forschungsprojektes konnte die positive Wirkung der Nachbehandlung auf die Lebensdauer von Schweißkonstruktionen nachgewiesen werden.
An der Universität Duisburg Essen konnte bei Versuchen[12] eine Verdoppelung der Ermüdungsfestigkeit und eine Erhöhung der Lebensdauer um den Faktor 10 gegenüber dem unbehandelten Ausgangszustand ermittelt werden.
An der finnischen Universität in Aalto erforscht ein Team um Prof. Gary B. Marquis seit Jahren den Nutzen des hochfrequenten Hämmerns. Im "International Journal of Fatigue" veröffentlichte er vor Kurzem einen Bericht[23] mit Vorschlägen für SN-Kurven, die konservativ in Bezug auf die verfügbaren Ergebnisse aus 228 Versuchen sind.
Verfahrensschritte[Bearbeiten | Quelltext bearbeiten]
Das HiFIT-Verfahren kann sowohl an bestehenden als auch an neuen Stahlkonstruktionen angewandt werden. Für eine gezielte Bearbeitung ist jedoch die Sichtbarkeit und Zugänglichkeit des Schweißnahtüberganges in den zu behandelnden Bereichen erforderlich. An Probeblechen oder in unbeanspruchten Bereichen des Grundmaterials wird die erforderliche Schlagintensität anhand der Spurtiefe ermittelt. Bestehende Konstruktionen müssen in der Regel vorab am Schweißnahtübergang eine Oberflächenvorbehandlung erhalten. Die Teile müssen frei von losem Rost und alten Farben sein. Gegebenenfalls ist vorheriges Sandstrahlen erforderlich. Für neue Konstruktionen ist keine besondere Vorbereitung erforderlich.
Das HiFIT-Gerät wird per Hand auf den zu behandelnden Schweißnahtübergang aufgesetzt und während der Behandlung an diesem entlanggeführt. Das Gerät arbeitet dabei mit einer Druckluftversorgung von 6–8 bar. Durch lokale Umformungen wird der Schweißnahtübergang plastisch verformt (ausgerundet) und verfestigt. Die Tiefe der Nachbehandlungsspur sollte zwischen 0,2 und 0,35 mm betragen. Die Einbrandkerbe am Schweißnahtübergang ist nach der Behandlung nicht mehr zu erkennen.
Durch Sichtkontrolle kann der behandelte Bereich untersucht werden. Die Behandlungsspur wird mit einer speziellen Schablone geprüft. Eine digitale Anzeige des Arbeitsdrucks ermöglicht dem Anwender jederzeit die Kontrolle.
Wirtschaftliche Bedeutung[Bearbeiten | Quelltext bearbeiten]
Das wirtschaftliche Potenzial von HiFIT-Behandlungen wird im REFRESH-Forschungsbericht[22] ausführlich behandelt. Im Folgenden werden die wichtigsten Punkte kurz genannt.
Lebensdauerverlängerung[Bearbeiten | Quelltext bearbeiten]
Bei Anwendung an bestehenden Bauwerken kann die Lebensdauer deutlich verlängert werden. Sofern keine makroskopisch erkennbaren Risse vorhanden sind, ist HiFIT ein sehr gut geeignetes Sanierungswerkzeug. Bei rechtzeitiger Sanierung bestehender Konstruktionen besteht nahezu kein Unterschied zur Lebensdauer neuer behandelter Schweißnähte. Hieraus ergibt sich das Potenzial, bestehende Konstruktionen weit über die bisherige Lebensdauer hinaus zu nutzen. Angewandt wird das HiFIT-Verfahren sehr effizient z. B. bei Autobahn-Brücken in Stahl-Hohlkasten-Profilbauweise bei laufendem Betrieb. Die Kosten für die Sanierung sind im Vergleich zu herkömmlichen Verfahren gering. Im Nutzfahrzeugbau und anderen Branchen werden hochbelastete Schweißnähte an bestehenden und neuen Konstruktionen zur Steigerung der Lebensdauer erfolgreich behandelt.
Erhöhung des übertragbaren Lastniveaus[Bearbeiten | Quelltext bearbeiten]
Bei Neukonstruktionen und bei einigen bestehenden Konstruktionen kann bei gleicher Lebensdauer das Lastniveau für die behandelten Schweißnähte erhöht werden. Bei gleicher Lebensdauer sind etwa die 1,6-fachen Lasten über die Schweißnaht übertragbar. Dies hat z. B. im Kranbau den äußerst positiven Effekt, dass größere Hublasten bewegt werden können. Die Effizienz der Kräne steigert sich mit jedem Hub.
Leichtbau[Bearbeiten | Quelltext bearbeiten]
Bei Berücksichtigung des HiFIT-Verfahrens während der Entwicklung, kann die Konstruktion, bei gleichem Lastniveau und gleicher Lebensdauer, gezielt verschlankt werden. Umfangreiche experimentelle Untersuchungen an Kerbdetails und FEM-gestützte Bemessungsverfahren zeigen die hohe Effizienz bei herkömmlichem S235, S355J2 und Feinkornstählen wie S460N, S690QL und noch höherfesten Stählen. Die erzielbaren Materialeinsparungen machen die Anwendung des HiFIT-Verfahrens in den meisten Anwendungen bereits wirtschaftlich sinnvoll. Bedenkt man zusätzlich noch den aus der Anwendung erzielten Gewichtsvorteil, erhöht sich z. B. die erreichbare Nutzlast im Fahrzeugbau.
Wirkungsweise[Bearbeiten | Quelltext bearbeiten]
Beim MHP schlägt ein zumeist kugeliges Hämmerwerkzeug mit hoher Frequenz auf eine Werkstückoberfläche. Dabei wird das Hämmerwerkzeug zum Beispiel von einem Roboter oder einer Bearbeitungsmaschine entlang der Werkstückoberfläche verfahren, so dass eine Reihe bzw. ein Feld von plastischen Eindrücken entsteht. Als Antrieb für das Hämmerwerkzeug werden aktuell elektromagnetische, pneumatische und piezoelektrische Systeme verwendet.[24] Wird das mit der Frequenz f oszillierende Hammerwerkzeug gegen eine metallische Oberfläche geführt, wird die kinetische Energie E des Hammerwerkzeugs beim Auftreffen in eine elasto-plastische Umformarbeit umgewandelt. Nach Entlastung des Kontakts, z.B. beim Rückhub, verbleibt ein der Geometrie des Hammers entsprechender plastischer Eindruck auf der Oberfläche.[25] Durch die plastische Deformation werden Oberflächenrauheiten eingeglättet. Gleichzeitig werden eine Kaltverfestigung und Druckeigenspannungen induziert. Frequenz und Bearbeitungsgeschwindigkeit definieren den Abstandes zwischen den Eindrücken. Hierdurch können sowohl sehr glatte als auch definiert strukturierte Oberflächen erzeugt werden.[26]

Verfahrensvarianten[Bearbeiten | Quelltext bearbeiten]
Zur Erzeugung der oszillierenden Bewegung können aktuell vier Erregertechnologien verwendet werden.
Bei dem pneumatischen System (P-MHP) wird durch Anlegen eines Luftstroms ein innerhalb des Werkzeugsystems beweglicher Kolben in Oszillation versetzt, der seine Bewegungsenergie auf den Stößel bzw. das Hammerwerkzeug überträgt. Vorteilhaft an der pneumatischen Verfahrensvariante sind die hohe Zuverlässigkeit und die einfache Bedienung. Als nachteilig können je nach Anwendungsfall die fehlende Möglichkeit zur Einstellung der Oszillationsfrequenz und der dauerhafte Kontakt des Hammerwerkzeugs mit der Oberfläche angesehen werden.[27]

Beim elektro-mechanischen Hammersystems (E-MHP) erfolgt die Erregung des Stößels durch Anlegen einer elektrischen Spannung an eine mit dem Stößel verbundenen Spule, welche infolge eines Magnetfeldes eines darum positionierten Dauermagneten ähnlich eines Lautsprechers in definierte Oszillation versetzt wird. Vorteile des E-MHP sind die zwischen 20 und 500 Hz einstellbare Frequenz und die hohe Schlagenergie. Dies ermöglicht eine vielfältige Anwendung und Erzeugung maßgeschneiderte Oberflächen auch bei hochfesten Werkstoffen. Als nachteilig können je nach Anwendungsfall die aufwendige Inbetriebnahme und der benötigte Bauraum angesehen werden.[28]

Beim „Piezo-Peening“ wird der Hammerkopf durch einen mit einer hohen, pulsierenden Gleichspannung beaufschlagten Piezokristall zum Schwingen gebracht. Die Schwingungen sind erzwungen. Die Anregung des Piezokristalls erfolgt typischerweise durch Hochspannungsverstärker. Bedingt durch die kontrollierbare Versuchsführung sind die erreichten Randschichtzustände gut reproduzierbar. Typische Bearbeitungsfrequenzen liegen bei 200 - 500 Hertz und typische Amplituden bei 10 - 20 µm. Eine funktionsfähige Versuchsanlage befindet sich am Karlsruher Institut für Technologie.[29]

Beim (rein) mechanischen Hämmern ist keine externe Energiezuführung notwendig. Der mechanische Antrieb erfolgt durch die rotierende Maschinenspindel und ist vergleichbar mit dem Antriebskonzept eines Schlagbohrers bzw. Bohrhammers. Mechanische Anstriebskonzepte erreichen eine Schlagenergie von 50 mJ bis maximal 2000 mJ und eine maximale Schlagkraft von 1000 N bis maximal 8000 N. Dabei oszilliert der Hammer mit einer Schlagfrequenz zwischen 330 und 400 Hz und bis 225 - 300 Hz bei höherer Schlagkraft. Dies ermöglicht Druckeigenspannungen bis ca. 800 MPa und Druckeigenspannungstiefen (Nulldurchgang) bis 4,5 mm (Werkstoff: Inconel 718, ausgelagert, Rp0,2 = 827 MPa).[30]
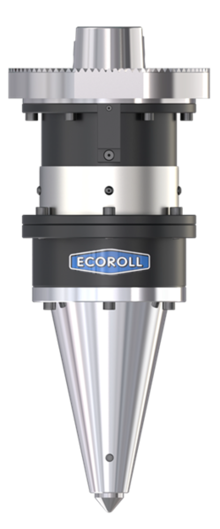
Anwendungsfälle[Bearbeiten | Quelltext bearbeiten]
Industriell weit verbreitet sind momentan das pneumatische und elektro-mechanische Hämmerprinzip. Beide werden überwiegend in der Automobilindustrie zum Glätten von Ziehwerkzeugen eingesetzt. Jedoch erhalten beide Verfahren aktuell auch Einzug in weitere Branchen, in denen eine Glättung der Komponenten (z.B. Kunststoffspritzgussindustrie), eine Strukturierung von Oberflächen (z.B. hydrodynamische Gleitlagerindustrie), eine Kaltverfestigung sowie eine Induktion von Druckeigenspannungen (z.B. Turbinenschaufel) von Vorteil sind.


Glättung von Werkzeugoberflächen[Bearbeiten | Quelltext bearbeiten]
Die maschinelle Glättung von Ziehwerkzeugoberflächen ermöglicht zum einen eine Steigerung der Prozessstabilität und zum anderen die Verkürzung der Prozesskette. Dies wurde beispielhaft am Werkzeugbau eines Automobilisten gezeigt.[31]
Reduktion von Reibung und Verschleiß[Bearbeiten | Quelltext bearbeiten]
Durch die definierte Einbringung von Oberflächenstrukturen können hydrodynamische Schmierstofftascheneffekte ausgenutzt werden, wodurch sich Reibung und Verschleiß beim Tiefziehen[32] oder bei Gleitlageranwendungen[33] (z.B. Nockenwellen) reduzieren lassen.
Steigerung der Biegewechselfestigkeit[Bearbeiten | Quelltext bearbeiten]
Durch die Induktion von Druckeigenspannungen und Kaltverfestigung führt das maschinelle Oberflächenhämmern zu einer gesteigerten Biegewechselfestigkeit verglichen mit dem ungehämmerten Zustand.[34]
Einordnung in die Gruppe der mechanischen Oberflächenbehandlungen[Bearbeiten | Quelltext bearbeiten]
Das maschinelle Oberflächenhämmern gehört wie z. B. Kugelstrahlen oder Festwalzen zur Gruppe der mechanischen Oberflächenbehandlungen. Diese Verfahren führen durch wiederholte lokale plastische Umformung der Werkstückoberfläche zu einer Verbesserung der Oberflächen und Randschichteigenschaften.
Beim Kugelstrahlen wird das Strahlmittel meist mittels Schleuderrad- oder Druckluft-Strahlanlagen beschleunigt und gegen die zu behandelnde Oberfläche geschleudert. Die Auftreffpunkte der einzelnen Elemente des Strahlmittels sind hierbei nicht definiert. Zur Angabe, wie oft ein Punkt auf der Oberfläche vom Strahlmittel getroffen wird, zieht man als Kennwert den Überdeckungsgrad heran. Ein weiteres, mit dem maschinellen Oberflächenhämmern verwandtes Verfahren ist das Festwalzen. Das Festwalzen zeichnet sich durch einen kontinuierlich aufgebrachten Walzdruck auf die Oberfläche und die damit einhergehende Deformation oberflächennaher Randschichten aus. Hierbei ist ein einfaches Überrollen, aber auch ein mehrfaches Überrollen einer Walzenbahn möglich. Die auftretenden Drücke und Reaktionskräfte am Werkzeug erfordern eine sehr steife Ausführung der Werkzeugaufnahme.
Wie bei den genannten Verfahren kommt es auch beim maschinellen Oberflächenhämmern während des Kontakts zwischen Hammerkopf und Werkstück zu einer Überschreitung der Fließgrenze des Werkstoffs und damit zu einer plastischen Umformung. Der Vorteil des Verfahrens besteht darin, dass die beschriebenen Effekte kontrolliert und deterministisch in der Randschicht des Werkstücks hervorgerufen werden können. Im Gegensatz zu den voranstehend genannten Verfahren kann ein Hämmerwerkzeug sehr gut in Bearbeitungszentren und robotergestützte Prozessketten integriert werden. Der Grund hierfür liegt in der Einfachheit der Werkzeuge zum maschinellen Oberflächenhämmern. Meist reicht eine Druckluft- oder Stromversorgung zum Betrieb der am Markt befindlichen Werkzeuge aus. Über die Verfahrensparameter des Hämmerns ist auch lokal eine gezielte Einstellung bzw. Verteilung der Bearbeitungsintensität gegeben. Unter Verwendung von speziellen, mit einer Mikrospitze versehenen Hammerköpfen ist es außerdem möglich während des Bearbeitungsprozesses Mikrostrukturen in die Werkstückoberfläche einzubringen. Diese dienen beim späteren Gebrauch des bearbeiteten Werkstücks als Schmierstoffreservoirs und verbessern die tribologischen Eigenschaften der Oberfläche zusätzlich.
Forschung, Entwicklung und Normung[Bearbeiten | Quelltext bearbeiten]
MHP wird heute erfolgreich in der Industrie angewendet. Da es sich um ein vergleichsweise neues Metallbearbeitungsverfahren handelt, ist es aktuell (2016) Gegenstand zahlreicher Forschungsprojekte. In Deutschland wird das P-MHP durch das Institut für Produktionstechnik und Umformmaschinen der TU Darmstadt erforscht. Das E-MHP wird sowohl vom PtU als auch vom Werkzeugmaschinenlabor der RWTH Aachen University untersucht. Das IAM-Werkstoffkunde in Karlsruhe widmet sich intensiv dem Piezo-Peening. Am Institut für Fertigungstechnik und Hochleistungslasertechnik IFT an der TU Wien werden ebenfalls P-MHP und E-MHP untersucht.

Jährlich findet gegen Ende des Jahres Forum statt, welches die Anwender des MHP aus Industrie und Forschung zusammenführt und anhand von Vorträgen aus Industrie und Forschung über den Stand der Technik informiert. Dabei wechselt der sogenannte Workshop Machine Hammer Peening (wMHP) im Turnus zwischen Darmstadt, Wien, Aachen und Karlsruhe.
Aus den Tätigkeiten der Workshop-Mitglieder ist ein VDI-Gremium zum Thema Oberflächenhämmern entstanden. Ziel des VDI-Gremiums war die Erstellung einer VDI-Richtlinie zur Standardisierung der Begrifflichkeiten und Beschreibung der Verfahrenseigenschaften. Die VDI-Richtlinie wurde am 3. Dezember 2015 durch das VDI-Gremium verabschiedet.
Siehe auch[Bearbeiten | Quelltext bearbeiten]
- Glattwalzen
- High Frequency Impact Treatment
- Pneumatic Impact Treatment
- Kugelstrahlen
- Richten (Fertigungsverfahren)
- Kaltumformung
- Schachtbau Nordhausen
Literatur[Bearbeiten | Quelltext bearbeiten]
- Steitz, M. (2016). Tribologisch günstige Oberflächenstrukturierung von Tiefziehwerkzeugen mittels maschinellem Oberflächenhämmern. PhD-Thesis TU Darmstadt (ptu). In press.
- Trauth, D. (2016). Tribology of Machine Hammer Peened Tool Surfaces for Deep Drawing. PhD-Thesis TU Aachen (wzl). Print. eBook.
- Habersohn, C. (2015). Analytische und simulative Betrachtung eines Oberflächenhämmerprozesses. PhD-Thesis TU Wien (ift). PDF.
- Lechner, C. (2014). Oberflächenmodifikation Unter Einsatz Der Technologie Des Schlagverdichtens (Machine Hammer Peenings). PhD-Thesis TU Wien (ift). PDF.
- Wied, J. (2011). Oberflächenbehandlung von Umformwerkzeugen durch Festklopfen. PhD-Thesis TU Darmstadt (ptu). PDF.* FOSTA Forschungsvereinigung Stahlanwendung e.V. (Hrsg.): REFRESH - Lebensdauerverlängerung bestehender und neuer geschweißter Stahlkonstruktionen. Ausgabe 2011, ISBN 978-3-942541-03-9 (Webseite des Projekts REFRESH auf den Seiten des Karlsruher Institut für Technologie).
- Stahlbau. 78. Jahrgang, September 2009, ISSN 0038-9145, A6449.
- IIW Recommendations for the HFMI Treatment For Improving the Fatigue Strength of Welded Joints. Autoren: Gary B. Marquis, Zuheir Barsoum, http://www.springer.com/de/book/9789811025037
Weblinks[Bearbeiten | Quelltext bearbeiten]
Einzelnachweise[Bearbeiten | Quelltext bearbeiten]
- ↑ Groche, P.; Steitz, (2011). Prozesskettenverkürzung im Werkzeugbau – Integration von Verfahren der maschinellen Oberflächeneinglättung. In: Werkstatttechnik online: wt, Springer VDI Verlag, Düsseldorf, 101 (10) pp. 655–659
- ↑ Radaj D., Vormwald M.: Ermüdungsfestigkeit, 3. Auflage, Springer Verlag, 2007.
- ↑ Forschungskuratorium Maschinenbau: Rechnerischer Festigkeitsnachweis für Maschinenbauteile aus Stahl, Eisenguss- und Aluminiumwerkstoffen, 6. Auflage. Frankfurt am Main, VDMA-Verlag, 2012.
- ↑ a b Hobbacher A.: IIW Recommendations for Fatigue Design of Welded Joints and Components, WRC Bulletin 520, The Welding Research Council, New York, 2009.
- ↑ a b Haagensen P. J., Maddox S. J.: IIW Recommendations On Methods for Improving the Fatigue Strength of Welded Joints, Woodhead Publishing, 2013.
- ↑ Gerster P.: Erhöhung der Lebensdauer bzw. der Ermüdungsfestigkeit durch Schweißnahtnachbehandlung, der praktiker, Vol. 9, pp. 302-310, 2009.
- ↑ Yildirim H., Marquis G.: Overview of fatigue data for high frequency treated welded joints, Welding in the World, vol. 56, pp. 82-96, 2012.
- ↑ Marquis G., Mikkola E., Yildirim H., Barsoum Z.: Fatigue strength improvement of steel structures by high-frequency mechanical impact: proposed fatigue assessment guidelines, Welding in the World, vol. 57, pp. 803-822, 2013.
- ↑ Marquis G., Barsoum Z.: Fatigue strength improvement of steel structures by high-frequency mechanical impact: proposed procedures and quality assurance guidelines, Welding in the World, vol. 58, pp.19-28, 2014.
- ↑ Leitner M., Stoschka M., Eichlseder W.: Fatigue enhancement of thin-walled high-strength steel joints by high frequency mechanical impact treatment, Welding in the World, Vol. 58, No. 1, pp. 29-39, 2014.
- ↑ Yildirim H., Marquis G.: Overview of Fatigue Data for High Frequency Treated Welded Joints, IIW-Document XIII-2362r1-11, 2011.
- ↑ a b c Berg J., Stranghöner N.: Ermüdungsverhalten HFH-nachbehandelter Kerbdetails des Mobilkranbaus, Stahlbau 83, Heft 8, 2014. Referenzfehler: Ungültiges
<ref>
-Tag. Der Name „Berg“ wurde mehrere Male mit einem unterschiedlichen Inhalt definiert. - ↑ Gerster P.: In der Praxis bewährt: Instandhaltung und Reparatur von Schweisskonstruktionen durch höherfrequentes Hämmern, der praktiker, Vol. 9, pp. 336-339, 2010.
- ↑ Gerster P., Schäfers F., Leitner M.: Pneumatic Impact Treatment (PIT) – Application and Quality Assurance, IIW-document XIII-WG2-138-13, 2013.
- ↑ Gerster P., Schäfers F.: Verfahren zur Erhöhung der Lebens- bzw. Ermüdungslebensdauer von Bauteilen, Stahlbau 83, Heft 8, 2014.
- ↑ Leitner M., Stoschka M., Fössl T., Eichlseder W.: Schwingfestigkeit hochfester Stähle an geschweißten Strukturen, Schweiss- und Prüftechnik, No. 1/2012, pp. 12-17, 2012.
- ↑ Schäfers F.: Hohe Druckeigenspannungen reduzieren Anlagenausfälle, Maschinenmarkt 22, pp. 56-59, 2011.
- ↑ Gerster P., Leitner M., Stoschka M.: Praktische Anwendungen eines höherfrequenten Hämmerverfahrens (PIT) in der Industrie, Proceedings of the Join-Ex Congress, Vienna/Austria, pp. 101-112, 2012.
- ↑ Stranghöner N., Berg J., Butz C.: Erhöhung der Lebensdauer von Fahrbahnübergängen mit Hilfe des höherfrequenten Hämmerns, 17. DASt-Kolloquium, Deutscher Ausschuss für Stahlbau, Weimar/Germany, pp. 109-113, 2010.
- ↑ Gabrys U.: Empfehlungen für den Neubau und die Instandsetzung von Stahlwasserbauten, Tagungsband zur Großen Schweißtechnischen Tagung 2011, DVS-Berichte, pp. 61-66, 2011.
- ↑ Schäfers F.: Anti Aging mit dem Hammer, Fachzeitschrift Instandsetzung, 2011.
- ↑ a b c Gregor Nüsse: REFRESH - Lebensdauerverlängerung bestehender und neuer geschweißter Stahlkonstruktionen. Verl. und Vertriebsges., Düsseldorf 2011, ISBN 978-3-942541-03-9.
- ↑ Halid Can Yildirim, Gary B. Marquis: Fatigue strength improvement factors for high strength steel welded joints treated by high frequency mechanical impact. In: International Journal of Fatigue. Band 44, November 2012, S. 168–176, doi:10.1016/j.ijfatigue.2012.05.002.
- ↑ Wied, J. (2011). Oberflächenbehandlung von Umformwerkzeugen durch Festklopfen. PhD-Thesis TU Darmstadt.
- ↑ Lechner, C. (2014). Oberflächenmodifikation Unter Einsatz Der Technologie Des Schlagverdichtens (Machine Hammer Peenings).
- ↑ Oechsner, M; Wied, J; Stock, J (2014). Influence of Machine Hammer Peening on the Tribology of Sheet Forming. In: Advanced Materials Research, Vols. 966-967, pp. 397-405.
- ↑ Wied, J. (2011)
- ↑ Lechner, C. (2014)
- ↑ Lienert, F.; Hoffmeister, J.; Schulze, V. (2013). Residual Stress Depth Distribution after Piezo Peening of Quenched and Tempered AISI 4140. In: Materials Science Forum, Vols. 768-769, pp. 526-533
- ↑ Produktflyer Fa. Ecoroll, Stand: 22.08.2016, vorerst erhältlich bei mail@ecoroll.de
- ↑ Groche, P.; Steitz, (2011).
- ↑ Steitz, M; Stein, P.; Groche, G. (2015). Influence of Hammer-Peened Surface Textures on Friction Behavior. In: Tribology Letters, 02, pp. 1-8.
- ↑ Trauth, D.; Feuerhack, A.; Mattfeld, P.; Klocke, F. (2015a). Analysis of the velocity distribution of an elliptic surface structure manufactured by machine hammer peening. In: Tribology Letters 60(19) pp. 18-31
- ↑ Trauth, D.; Klocke, F.; Welling, D.; M. Terhorst; Mattfeld, P.; Klink, A. (2015b). Investigation of the Surface Integrity and Fatigue Strength of Inconel718 after Wire EDM and Machine Hammer Peening. In: International Journal of Material Forming.